Cap a la planta autònoma: la digitalització com a catalitzador del canvi industrial
En l’actual context de transició energètica i pressió competitiva global, la indústria química afronta una transformació profunda i irreversible. La digitalització i la sostenibilitat han deixat de ser opcions estratègiques per convertir-se en eixos fonamentals del model industrial del segle XXI. Aquest enfocament s'ha fet evident durant la jornada “Eines digitals per avançar cap a la planta autònoma sostenible”, organitzada per la Comissió d’Indústria Química d'Enginyers Industrials de Catalunya, amb la participació d’empreses líders com Technip Energies, Repsol i Schneider Electric.
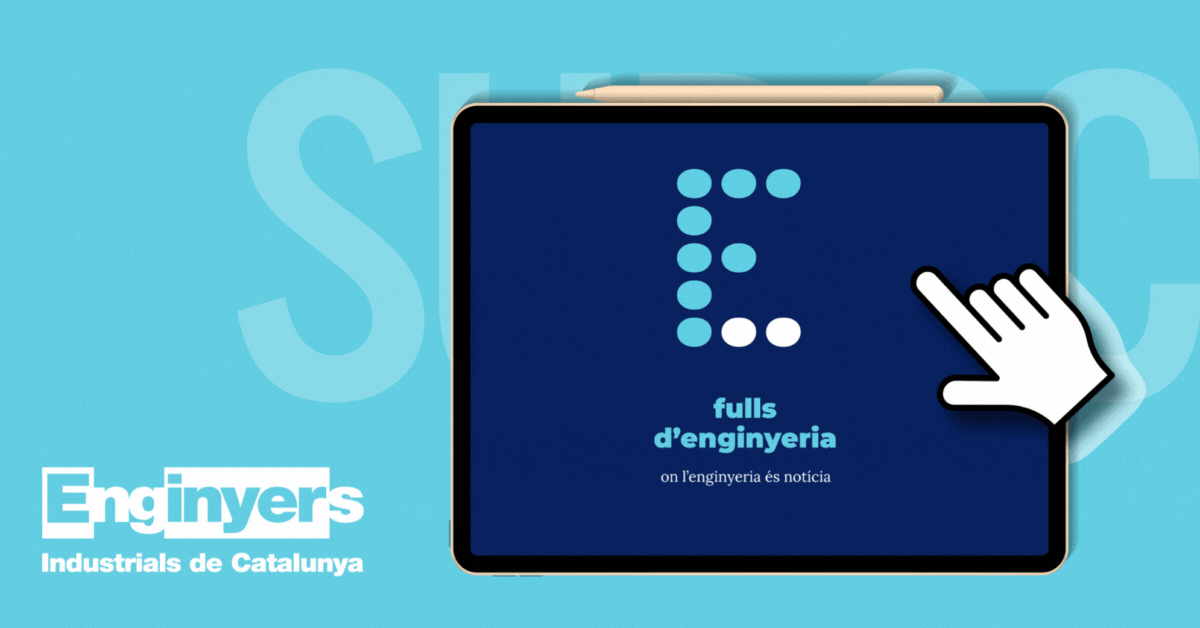
Durant la sessió, s'ha posat de manifest com les plantes industrials estan evolucionant cap a sistemes altament automatitzats, intel·ligents i energèticament eficients. Aquest nou model d’operació permet reduir la intervenció humana directa i alliberar el talent tècnic per dedicar-lo a tasques de més alt valor afegit. La convergència entre robòtica, intel·ligència artificial, bessons digitals i ciberseguretat ha obert la porta a instal·lacions més flexibles, segures i sostenibles, capaces d’adaptar-se de forma autònoma a un entorn industrial en constant canvi.
Fabrice Rey, responsable de Digital Asset Performance a Technip Energies, ha exposat com la companyia ha desplegat el concepte de Normally Unattended Installation (NUI), un nou paradigma de planta industrial capaç de funcionar amb mínima presència humana. Aquest model es fonamenta en l’ús de bessons digitals, robotització, monitoratge remot i una arquitectura simplificada, orientada a la fiabilitat i el baix manteniment.
Tal com ha explicat Rey, el sistema es basa en centres remots dotats de sistemes DCS, des d’on operadors i especialistes prenen decisions en temps real. Les dades de la planta es recullen amb alts nivells de ciberseguretat, es processen mitjançant models digitals avançats i es fan servir per alimentar simuladors i llançar missions robòtiques quan calgui. Aquesta estratègia permet anticipar avaries, ajustar operacions automàticament i optimitzar recursos amb un alt grau d’eficiència.
Repsol, per la seva banda, ha definit una estratègia molt clara cap a la planta autònoma, segons ha explicat Jose María Montserrat, director de Processos Avançats. Aquesta estratègia es construeix sobre dos grans pilars: l’eficiència industrial i la transició energètica. A través de tecnologies madures i una gestió avançada dels actius, l’empresa ha iniciat una profunda transformació del seu model operatiu. Montserrat va destacar la implantació d’optimitzadors de llaç tancat, que permeten l’autooptimització dels processos en diversos punts crítics.
Quan aquesta automatització no és viable, s’utilitzen sistemes de llaç obert que ofereixen recomanacions intel·ligents als operadors. A més, Repsol ha desenvolupat bessons digitals del procés, capaços de simular escenaris operatius en temps real i respondre preguntes com “què passa si augmento la temperatura?” o “quant em queda de vida útil del catalitzador?”. Aquesta capacitat d’interacció amb el sistema representa un avenç significatiu en el control i optimització de les plantes.
Repsol ha desplegat múltiples projectes dins d’aquesta estratègia, des de la robotització de tasques manuals fins al monitoratge amb càmeres i drons, passant pel desenvolupament de bessons digitals i la integració de sistemes intel·ligents de manteniment predictiu. El conjunt d’aquestes iniciatives conforma el seu Full de Ruta cap a la Planta Autònoma, amb l’objectiu de reduir riscos laborals, millorar la disponibilitat dels actius i garantir una operació eficient, segura i desassistida.
En la mateixa línia d’innovació, Schneider Electric ha mostrat el valor de l’Advanced Process Control (APC) com a eina clau per a la millora contínua del rendiment de les plantes. Manuel Járrega, APC EMEA Commercial Leader de l’empresa, ha explicat que l’APC permet capturar la dinàmica real dels processos mitjançant models predictius multivariables.
Aquesta capacitat de modelatge permet optimitzar el consum energètic, millorar la qualitat dels productes i reduir l’impacte ambiental. A través de la plataforma EcoStruxure APC, Schneider ha implantat més de 300 solucions a escala mundial, amb casos d’èxit com la reducció del 25% d’amoníac en efluents, un 10% menys en el flux d’aire i un increment del 25% en l’eficiència dels sistemes de tractament d’aigües.